To support off-shore operations, for example, helicopters must be big enough to manage adverse weather and able to carry as many as two dozen crew members, plus their equipment, to rigs moored in deep water.
However, the opposite is true for fume extractors used for maintenance welding on the rigs.
These air filtration devices are designed to protect welders from toxic fumes created by their torches. Because they are transported to rigs on helicopters and once on the rig are used in confined spaces, the perfect fume extractor for maintenance welding must be small yet powerful.
Varied materials, varied airborne hazards
Maintenance welding is a standard rig activity and is quite varied. A maintenance welder may work on heavy equipment, large vessels designed to hold liquids and gases, valves, and high-pressure pipes.
The materials they weld vary, too, and may include aluminum, stainless steel and carbon steel.
Heating these metals with a torch produces hazardous fumes that can cause short-term ailments as well as chronic illness.

Stainless steel is distinctive, however, in that the high heat of welding produces hexavalent chromium — referred to as hex chrome — an oxidized version of chromium heavily regulated by OSHA because it is a carcinogen.
Chromium can also be found in welding flux and some coatings applied to metals. Additional respiratory hazards are found in non-metallic polymers, often applied as insulation to pipes.
Even if the torch never directly hits the coatings, hot metal radiates heat that thermally decomposes polymers, releasing chemical molecules that, like hex chrome particles, become airborne and shouldn’t be inhaled.
Tough tests provide confidence
Controlling hex chrome particles in welding environments is crucial for the health and safety of oil and gas welders. We asked industrial hygienists to test the ability of the Model 300 welding fume extractor to remove hex chrome particles from workplace air. Their efficiency tests documented a 99.9% reduction of hex chrome.1
Due to emerging nanotechnologies, heated coatings and paints may now produce an additional respiratory hazard because nano-scale ingredients [measured in one billionth of a meter] are frequently added to industrial coatings to improve their coverage properties.
The Model 300 was included in NIOSH testing at a nanoparticle manufacturing facility. For the operation described, manganese in workplace air was reduced by 96%, silver by 75%, and cobalt by 94%.2
Fumes captured at the source
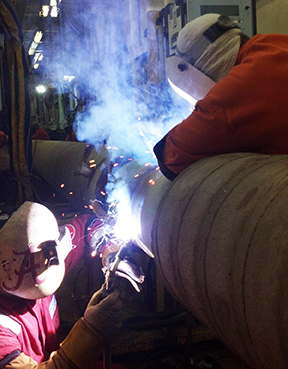
With no fume extractor in sight, two welders produce copious smoke as they weld pipe on a rig designed to lay an ultra-deep-water pipeline.
Photo credit: kopf, offshore pics thread, failheap-challenge.com
Effective welding fume extraction means the fumes are captured at the torch, where they are created, before they spread.
This is particularly important in confined spaces, which are not conventional work spaces and may not have consistent ventilation.
A flexible python hose on the Model 300 Welding Fume Extractor can be snaked up ladders, down stairs and under vessels.
Its magnetic capture hood allows welders to adhere it to any ferrous metal surface close to the torch.
Hands remain free to work while fumes are pulled away from faces and into filters that trap the hazardous substances.
Variable air volume control, adjustable in small increments, allows welders to make adjustments based upon length of capture hose and the type of welding they are doing.
MIG and TIG welding, for example, use shielding gases that may be lighter than air or heavier than air.
Variable air volume allows welders to help keep the shielding gases where they are directed by their welding gun, with positive impact on the quality of the weld.
Appropriate fume extraction and air filtration allows welders to help protect themselves and their welding bead.
Size, modularity meet helicopter requirements
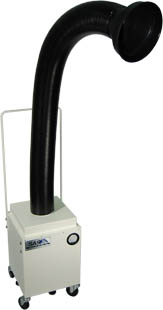
Sentry Air Systems Model 300 Portable Fume Extractor, an engineering safety control that removes airborne contaminants, including nanoparticles, from workplace air.
The Model 300 is a welding fume extractor appropriate for helicopter transport.
It weighs just 40 pounds. Handle detached, its dimensions are roughly 16” x 13” x 16”. Hoses are stuffed into duffle bags and stowed wherever they fit.
These modular qualities are important to helicopter pilots, who must comply with weight distribution requirements and must be able to distribute equipment components within the cabin to meet them.
Compact size doesn’t mean miniaturized filtration performance.
Model 300s headed for confined space duty are shipped with HEPA filtration for particles and activated carbon filtration for chemical fumes, just like larger production welding fume extractors.
Replacement filters are boxed separately and are also easy to transport.
Looking for a small, powerful welding fume extractor?
Our applications specialists are happy to work with you to determine the right fume extractor for your applications.
Email sales@sentryair.com, call 800.799.4609 or use the comment form below or on our website pages.
Resources
1R. F. Adams and Associates, Inc. (2007), Industrial Hygiene Report, Control of Hexavalent Cr in Welding Fume for Sentry Air Systems
http://www.sentryair.com/specs/HexavalentChromTestApril19_2007.pdf
2Mark M. Methner (2008), Effectiveness of Local Exhaust Ventilation (LEV) in Controlling Engineered Nanomaterial Emissions During Reactor Cleanout Operations, Journal of Occupational and Environmental Hygiene
https://sentryair.com/blog/powder-containment/capturing-the-elusive-nanoparticle/
Not all oil and gas exploration takes place on a rig
https://sentryair.com/blog/laboratory-fume-control/not-all-oil-and-gas-exploration-takes-place-on-a-rig/