As the price tag decreases and the precision and accuracy increases, the incorporation of 3D printers in dental and orthodontic practices are becoming more prevalent.
For decades, dental professionals have been trained on the art of making molds, splints, partials, surgical drill patterns and a variety of other oral apparatuses.
The easiest way to describe this process begins with mold being taken of a patient’s mouth. Once the mold sets, it is sent to a dental lab where technicians form a cast out of the mold which becomes the base design of the oral apparatus. Once completed, the final product is sent back and fitted to the patient’s mouth.
The entire process can take anywhere from 2-3 weeks but if there are defects or the fit wasn’t correct, modifications would have to be made adding to the overall wait time.
The introduction of 3D printing technology dramatically changes the way these apparatuses are made. By fully digitizing the process, a scan can be made of the patient’s mouth without having to make a mold. The digital scan is then used to design the appropriate oral piece. That design is sent directly to the 3D printer that then produces an exact replica.
This drastically reduces wait time from weeks to mere hours, and increases overall production as more than one piece can be made at a time.
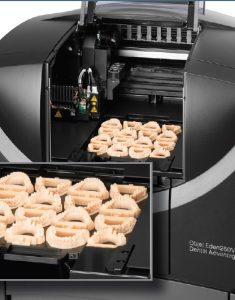
Stratasys VeroGlaze 3D Printing dental material in A2 teeth color is perfect for natural looking dental models with fine details and resolution.
Printers on the market today are able to produce life-like resemblance in detail, color, and strength. In fact, there are many case studies available describing how small dental practices were able to save money, time, and significantly increase the production of oral apparatuses simply by utilizing 3D printers.
If your practice is considering purchasing a 3D printer, or if you already use one, give careful consideration to a ventilation plan for your printer.
Why do you need ventilation?
Well, 3D printers emit ultra-fine particles (UFP) which are measured on the nanoscale and are invisible to the naked eye. Their microscopic size means that they easily become airborne.
Multiple studies on the effects of UFP inhalation have concluded that UFP has the ability to travel into the lungs and make its way into the head’s airways and into the brain. UFP also can accumulate in the bone marrow and other major organs leading to serious health effects.
If you plan on conducting 3D printing in an office setting, operators, workers, and even patients will be susceptible to UFP inhalation.
What exactly are you breathing?
Feedstock filament ― the material placed in the 3D printer to create your object ― gets heated during the printing process. It is during this process where microscopic fume and particulate (UFP) comes off of the material and emitted into the air.
The filaments used in dental 3D printing applications contain a variety of components. If you review the filament’s Safety Data Sheet you will see that a majority of components are proprietary. This means you will not know the exact chemicals used to create the filament; further reason as to why ventilation measures should be taken.
Although the exact mixture and ratio may be proprietary, common filaments are made of:
- Acrylic resins and fillers
- Acrylated monomers and oligomers
- Titanium dioxide
- 1, 6-Hexanediol acrylate
- 16-dioldimethacrylat
- Tetrhydrofurfuryl-2-methacrylat
- Methacrylated oligomer
- Urethane acrylate
Most 3D printers have an enclosed printing area with hinged door. During printing UFP accumulates within the enclosed area. Once the pieces are finished, the door is opened allowing UFP to escape into the air.
How to capture UFP and avoid inhalation.
Avoid exposing yourself, staff and patients to UFP by utilizing a fume extraction system with quality HEPA filtration.
Sentry Air Systems provides such systems and our variety of configurations allow for seamless incorporation into most workspaces.
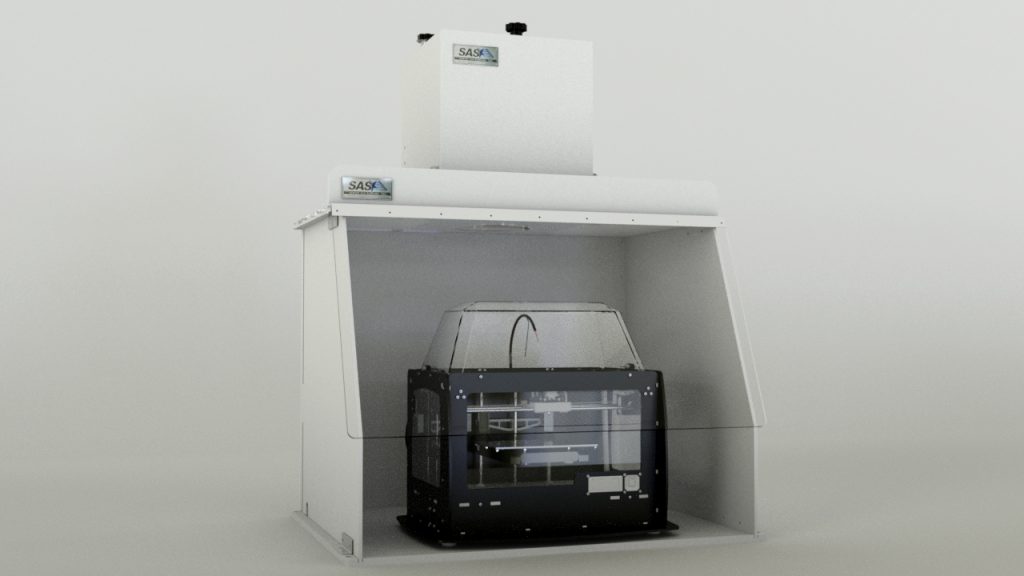
Our ductless containment hoods with HEPA filtration come in a variety of widths and can accommodate most desktop 3D printers.
In the picture above, an art class uses a ductless containment hood to not only arrest fumes created inside the hood, but to also duct two 3D printers into the filter chamber for maximum UFP capture.
A portable fume extraction system was used at a maker space. The “python-style” flex hose was piped into the exhaust port of the 3D printer.
Proven particle reduction.
Sentry Air Systems tested the above maker space exhaust system for particle efficiency. The below images depict the testing process.
Step 1: Used a particle scanner to see the number of particles in the ambient air approximately 3 feet from the 3D printer. The reading showed 72,400 particles per cubic foot down to 0.3 microns in size.
Step 2: Used a particle scanner to see the number of particles directly inside the 3D printer during operation. The reading showed 518,800 particles per cubic foot down to 0.3 microns in size.
Step 3: Used a particle scanner to see the number of particles being exhausted out of the fume extractor after being circulated through the HEPA filter chamber. The reading showed 0 particles per cubic foot down to 0.3 microns in size.
This means that the fume extractor was able to pull harmful UFP away from the 3D printer and into the filter chamber before recirculating filtered air back into the room.
Contact Us
For more information on fume extractors for 3D printing, give us a call at 800.799.4609, email sales@sentryair.com, or fill out the feedback form below. A Sentry Air technical applications specialist will be able to determine the most appropriate set up and configuration for you.