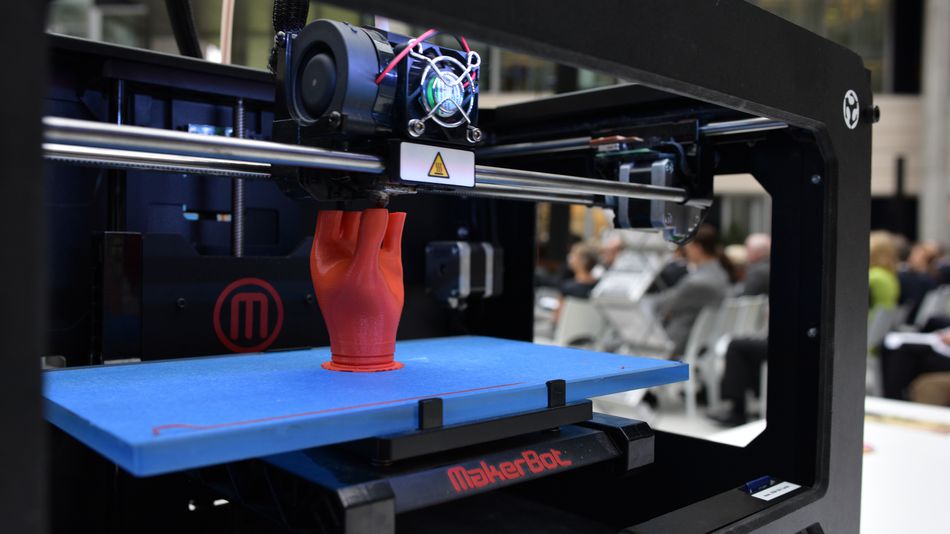
3D Printer (Source)
Nowadays, it is a common sight to see 3D printers in homes, schools, offices, labs, and workshops. The ability to quickly and economically print objects and prototypes make 3D printing one of the fastest-growing technologies today. The process of creating three-dimensional printed objects is actually quite interesting.
The majority of commercially available 3D printers utilize an additive manufacturing technique known as molten polymer deposition (MPD), whereby a solid thermoplastic filament is forced through a computer-driven extrusion nozzle. The heated nozzle melts the thermoplastic feedstock and deposits streams of extruded plastic in thin layers across a moving baseplate. As the material hardens and the base plate moves to the next layer, the three-dimensional solid shape is rapidly formed. (Stephens, Azimi, Orch, Ramos 2013)
Hazards of 3D Printing
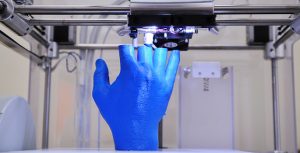
3D Printer in Progress (Source)
While 3D printing is a fun and exciting new technology, the basics of melting plastic to reform it into something new is an old processing technique. It should be noted here that several health and safety agencies, as well as independent researchers, have spent years studying the process of plastic thermal degradation and their subsequent health effects.
Only in the past few years have studies focused on plastic decomposition as it relates to 3D printing. Their findings are important in that measurable respiratory hazards are emitted during the 3D printing process and greater research should be done on this topic.
Many desktop 3D printers rely on heated thermoplastic extrusion and deposition, which is a process that has been shown to have significant aerosol emissions in industrial environments. (Stephens, Azimi, Orch, Ramos 2013)
While this article focuses on plastic-based 3D printing filaments and their associated health effects, we have included a sampling of other materials used in 3D printing. Limited research, if any, has been done on non-plastic-based filaments. However, similar precautions outlined in this article should be implemented when working with any type of 3D filament.
Examples of 3D printing filaments
Acrylonitrile Butadiene Styrene (ABS)* | Nylon | Polyvinyl Acetate (PVA) | Plasticized Copolyamide TPE (PCTPE) |
Polylactide Resin (PLA)* | Polycarbonate (PC) | High Density Polyethylene (HDPE) | Other polymers, metals, ceramics |
*Most popular filaments |
Chemical Health Hazards of Popular 3D Printing Filaments
ABS Filament
Comprised of three primary chemicals: acrylonitrile, butadiene, and styrene, ABS is one of the most popular filaments for 3D printing. Because of the popularity of this filament, it is important to discuss the studied properties, characteristics, and health effects involved when ABS undergoes thermal processing and decomposition.
To begin, all three of these components are listed as carcinogenic or possibly carcinogenic to humans according to the International Agency for Research on Cancer (IARC)
• Acrylonitrile – Possibly carcinogenic to humans
• Butadiene – Carcinogenic to humans
• Styrene – Possibly carcinogenic to humans
When exposed to melting temperatures, ABS polymers will begin to breakdown and one study identified up to 27 chemical compounds generated as a byproduct of ABS combustion.
In the case of ABS, twenty-seven chemical compounds have been identified as combustion products. It is obvious that more combustion products are generated, but have not been identified or investigated to date. The degradation products which appear to be of primary toxicologic concern are CO and HCN. (Rutkowski, Levin 1986)
What is particularly concerning about ABS decomposition is the quantity of styrene emitted. A 2016 study of ultrafine particle (UFP) emissions for multiple 3D printer and filament combinations found that the primary VOC emitted from ABS filament is styrene.
The predicted styrene concentration in this configuration would be approximately 20 times higher than the highest styrene concentration measure in a commercial building in the US EPA BASE study and more than 20 times higher than the average concentration in US residences. There are also reports that suggest exposure to styrene at these concentrations could be problematic for human health. (Azimi, Zhao, Pouzet, Crain, Stephens 2016)
Due to the negative health effects of styrene exposure, OSHA has placed strict limits on the permissible exposure level to workers. NIOSH recommends even further reduction in the exposure limits.
STYRENE EXPOSURE | ||
Agency | Exposure Limit | Side Effects |
OSHA
Permissible Exposure Limit |
TWA 100 ppm
Ceiling 200 ppm STEL 600 ppm |
Health effects from exposure to styrene may involve the central nervous system and include complaints of headache, fatigue, dizziness, confusion, drowsiness, malaise, difficulty in concentrating, and a feeling of intoxication |
NIOSH
Recommended Exposure Limit |
TWA 50 ppm
STEL 100 ppm |
PLA Filament
Polylactic Acid (PLA) is another thermoplastic that is widely used in 3D printing. While there is currently limited health and safety information regarding thermally-decomposed PLA, studies have shown that the thermoplastic still emits measurable amounts of ultrafine particles.
The operation of the two printers utilizing PLA as a feedstock increased concentrations primarily for particles larger than 20 nm. (Stephens, Azimi, Orch, Ramos 2013)
However, in the same study researchers found that ABS filament emitted much higher levels of UFP than its PLA counterpart.
The higher temperature ABS-based printers had total UFP emission rates nearly an order of magnitude higher than the lower temperature PLA-based printers. Peak emission rates from the PLA-based printers occurred in the 48-65 nm size range while peak emission rates from the higher temperature ABS-based printers occurred in a smaller size range (~15-49 nm). (Stephens, Azimi, Orch, Ramos 2013)
While PLA may be a better alternative to ABS in regards to ultrafine particles emission, caution should still be used to avoid overexposure.
Health Hazards of Ultrafine Particles (UFP)
Gases, fume, and ultrafine particles are all emitted during the 3D printing process due to the melting of the printer’s filament. While any type of emission may pose health risks, researchers are particularly concerned with ultrafine particles.
Moreover, ultrafine particles may be of particular importance for toxicity and fumes emitted from the melting of some thermoplastics (Stephens, Azimi, Orch, Ramos 2013).
A 2016 study of commercially available 3D printers sought to measure both the size and quantity of UFP emitted during the printing process. Researchers found that UFP levels spiked during particular printing time intervals.
Results […] are similar to results from most of the experiments in that UFP concentrations typically rapidly increased just after printing began and persisted for the first 10-20 minutes, then decreased to a lower level, albeit typically to a level that was still higher than the background concentration. During some tests with other printer and filament combinations, UFP concentrations peaked again near the end of the print period as the thin protrusions on the printed object were created. (Azimi, Zhao, Pouzet, Crain, Stephens 2016)
In 2013, a review panel from the Health Effects Institute (HEI) published an extensive report on UFP entitled: Understanding the Health Effects of Ambient Ultrafine Particles. In their report, HEI noted the unique health risks UFP pose when compared to larger particles.
Experimental studies have provided evidence to indicate that, as a result of their physical characteristics, inhaled UFPs differ from larger particles in their deposition patterns in the lung, their clearance mechanisms, and in their potential for translocation from the lung to other tissues in the body. Some animal studies have also demonstrated translocation of UFPs via the olfactory nerve to the brain. Taken together, these findings provide a rationale for the hypothesis that the adverse health effects of exposure to UFPs differ from those of larger particles. (HEI Review Panel on Ultrafine Particles. 2013)
Furthermore, “Observed effects in selected studies include lung function changes, airway inflammation, enhanced allergic responses, vascular thrombogenic effects, altered endothelial function, altered heart rate and heart rate variability, accelerated atherosclerosis, and increased markers of brain inflammation.” (HEI Review Panel on Ultrafine Particles. 2013)
In a joint effort study, researchers Merlo and Mazzoni partnered with WASP Project by CSP Sri to deepen their understanding of 3D printing health hazards in terms of healthiness in the workplace. In their report, they detail how nanoparticles travel through the human body. (Merlo, Mazzoni)
Recent studies have highlighted how nanoparticles are able to enter into human blood system in less than a minute. Once absorbed in the respiratory tract, skin and gastrointestinal tract, the particles may reach the systemic circulation and migrate successfully in different organs and tissues; in particular the organs that appear to be most vulnerable are the liver and the spleen, which perform a job of filtering toxic substances in the human body, aggravating their functionality. (Merlo, Mazzoni)
Additionally, “Various studies have shown that these diseases are related to oxidative stress caused by emissions of toxic substances that affect human cells accelerating their aging.” (Merlo, Mazzoni)
Protect Against Exposure to Ultrafine Particles and Fumes from 3D Printing
After reviewing several studies that focused on 3D printing, UFP, nanoaerosols, or a combination of the three, their findings are strikingly similar – precaution should be taken while operating UFP-emitting devices in poorly ventilated environments. Brief excerpts from these studies are below.
Given these findings, we are prompted to make the following recommendations […] in the absence of new low-emitting filaments, manufacturers should work to evaluate the effectiveness of sealed enclosures on both UFP and VOC emissions or to introduce combined gas and particle filtration systems. Until then, we continue to suggest that caution should be used when operating many printer and filament combinations in enclosed or poorly ventilated spaces or without the aid of gas and particle filtration systems. (Azimi, Zhao, Pouzet, Crain, Stephens 2016)
Long before the final conclusions of toxicology research studies, it is today necessary to apply the principle of precaution by implementing among other, efficient personal protections against the engineered nanoparticles in order to decrease the exposure […] Among all the tested filters the HEPA cellulose filter used in nuclear monitoring, the HEPA H14 and the ULPA U15, showed the best efficiency for smaller particles. – (Golanski, Guiot, Rouillon, Pocachard, Tardif 2009)
In this work, we present some of the first known measurements of which we are aware of UFP emissions from commercially available desktop 3D printers […] These results suggest caution should be used when operating some commercially available 3D printers in unvented or inadequately filtered indoor environments. – (Stephens, Azimi, Orch, Ramos 2013)
So far it is already possible to give some tips and suggestions, such as using the printers in ventilated places, even better if provided with an air exchange system with a primary power of at least 3 volumes of the room per hour. (Merlo, Mazzoni)
HEPA and ULPA Filtration for UFP
Larger particles (pollen, dust, spores, etc.) are measured in microns (micrometers). One micron is one-millionth of a meter and is expressed as millimeter or µm. Smaller particles that cannot be measured in the micron-scale often referred to as ultrafine particles (UFP), are measured in nanometers. One nanometer is one-billionth of a meter and is expressed as nm.
Historically, HEPA and ULPA filters are known to be excellent media for the capture of particles. While there are several types of HEPA and ULPA filters based on relative efficiency levels, the most common efficiencies used in industry are as follows:
• HEPA – Up to 99.97% efficient on particles down to 0.3 microns
• ULPA – Up to 99.9995% efficient on particles down to 0.12 microns
To better understand HEPA and ULPA filtration efficiencies, the below chart illustrates common particle sizes on the micron scale.
When discussing UFP, it is important to understand just how small they are in comparison to larger particles. For example, according to the chart above, a single pollen spore is approximately 10 microns (micrometer). That calculates to 10,000 nanometers. If a commonly used HEPA filter is only efficient down to particles that are 0.3 microns in size (300 nanometers), then how can we expect it to capture the even smaller nano-sized particles emitted during 3D printing?
A group of researchers investigated this question and their findings are published in a 2009 study entitled: Experimental evaluation of personal protection devices against graphite nanoaerosols: fibrous filter media, masks and protective clothing. In the study’s introduction, the researchers are reminded of already accepted particle behaviors and identify a possible loophole for nanoparticles:
According to conventional filtration theory, particles smaller than 100 nm are submitted to random displacements due to Brownian motion which enhances the collision probability with the fibers. The particles are then irreversibly captured by van der Waals forces. Nevertheless, the filtration efficiency to nanoparticles could be affected by the thermal rebound effect during filtration due to the particle bounce on the fiber filter. (Golanski, Guiot, Rouillon, Pocachard, Tardif 2009)
As part of their study, the researchers evaluated the effect of thermal rebound on the filtration efficiency of nanoparticles. Their findings suggest that not only does thermal rebound have minimal effect on fibrous filters, but that these filters may be more efficient than previously thought.
Moreover, no thermal bounce is observed until 10 nm. Consequently these filters are even more efficient for smaller nanoparticles than for 100 nm. Among all the tested filters the HEPA cellulose filter used in nuclear monitoring, the HEPA H14 and the ULPA U15 showed the best efficiency for smaller particles. (Golanski, Guiot, Rouillon, Pocachard, Tardif 2009)
3D Printing Fume and Particulate Control Solutions
Several of the studies referenced in this article mention particle and/or gas filters for UFP and VOC containment. The use of engineering safety controls during 3D printing will make a significant impact on the reduction of exposure to these emissions. Sentry Air Systems has been designing and manufacturing air filtration systems for more than 30 years. Our products are equipped with HEPA, ULPA, or granule activated carbon filters, or a combination of multiple filter types. Due to the modularity in our product design, we are able to accommodate all types of 3D printers whether big or small, open or closed printer beds.
Dual Python Portable Fume Extractor
At Axonic Modulation Technologies, the lab was experiencing a strong odor of chemicals throughout the room disrupting everyday work. Employees were complaining due to the smell but probably also suffering from health hazards.
The employees were able to attach the dual hose from a SS-300-PYT to the printer’s exhaust ports. They utilized both HEPA and Activated Carbon filters to cleanse the air removing it of harmful fumes, particles, and the strong odor. They run it 24 hours a day 7 days a week while printing to completely safeguard employee health.
This lab is very happy to have a ductless option as their building would not allow them to add air ducts and did not want to make the investment as well.
Single Hose Python Portable Fume Extractor
The Children’s Museum of Houston utilizes a Sentry Air Model 300 Python Fume Extractor [SS-300-PYT] in their Maker Annex at the 3D printing station. Once the fume extractor was installed on the 3D printer, we took particle measurements using a laser particle counter.
Inside Printer Cabinet Particle Count
The counter registered 518,800 particles per cubic foot inside the printer cabinet while it was printing. The particle scanner readings register at 0.3 microns and larger in particle size.
Outside Filter Output Particle Count
The fume extractor filter outlet releases cleansed air, after filtration by both a particle filter (HEPA) and a VOC filter (10 lb. activated carbon), and is redeposited to the room. The particle counter registered 0 particles per cubic foot (at 0.3 microns) for the duration of the 3D printing operation.
While a particle size of 0.3 microns (or 300 nanometers) is larger than recorded UFP emitted during 3D printing (<100 nm), HEPA and ULPA filters have been determined to be more efficient for particles of this size, as discussed earlier in this article.
Ductless Fume Hood
Small desktop 3D Printers can be completely contained to capture particles and fumes using a Ductless fume Hood. The picture on the left shows a 40″ Ductless fume hood with a small 3D Printer inside. This solution works best for small printers but does provide added protection by completely isolating the printer from the outside workspace.
More information about Sentry Air’s solutions to 3D printing fume control can be found on our website. We have application specialists ready to discuss your 3D application and work with you to find the most economical and efficient solution.
Contact Sentry Air
For more information about engineering safety controls for 3D printing operations or to receive a free quote, please contact Sentry Air at 800.799.4609, email sales@sentryair.com, visit our website or fill out our contact form.
Sentry Air Systems, Inc. provides this information as a customer service, but cannot be responsible for its accuracy or completeness. Consult competent legal authorities as well as safety and hygiene professionals.
Resources
Azimi, P., Zhao, D., Pouzet, C., Crain, N. E., & Stephens, B. (2016). Emissions of Ultrafine Particles and Volatile Organic Compounds from Commercially Available Desktop Three-Dimensional Printers with Multiple Filaments. Environmental Science & Technology Environ. Sci. Technol., 50(3), 1260-1268. doi:10.1021/acs.est.5b04983
Donaldson, K., Tran, L., Albert Jimenez, L., Duffin, R., Newby, D. E., Mills, N., . . . Stone, V. (2005, October 21). Combustion-derived nanoparticles: A review of their toxicology following inhalation exposure. Particle and Fibre Toxicology. Retrieved from http://particleandfibretoxicology.biomedcentral.com/articles/10.1186/1743-8977-2-10
Golanski, L., Guiot, A., Rouillon, F., Pocachard, J., & Tardif, F. (2009). Experimental evaluation of personal protection devices against graphite nanoaerosols: Fibrous filter media, masks, protective clothing, and gloves. Human & Experimental Toxicology, 28(6-7), 353-359. doi:10.1177/0960327109105157
HEI Review Panel on Ultrafine Particles. 2013. Understanding the Health Effects of Ambient Ultrafine Particles. HEI Perspectives 3. Health Effects Institute, Boston, MA.
Merlo, F., & Mazzoni, S. (n.d.). Gas evolution during FDM 3D printing and health impact. Retrieved from http://www.3dsafety.org/3dsafety/download/mf2015_eng.pdf
Rutkowski, J. V., & Levin, B. C. (1986). Acrylonitrile-butadiene-styrene copolymers (ABS): Pyrolysis and combustion products and their toxicity – a review of the literature. Fire Mater. Fire and Materials, 10(3-4), 93-105. doi:10.1002/fam.810100303
Stephens, B., Azimi, P., Orch, Z. E., & Ramos, T. (2013). Ultrafine particle emissions from desktop 3D printers. Atmospheric Environment, 79, 334-339. doi:10.1016/j.atmosenv.2013.06.050